Токарно-фрезерные обрабатывающие центры SPECTR TC
Ø обработки: 320 - 460 мм
РМЦ: 500 - 640 мм
Мощность: 11 / 15 - 15 / 18,5 кВт
Вес: 3200 - 4700 кг
- Револьверная голова SAUTER на 12 позиций
- Направляющие качения роликового типа по осям X, Z от PMI/THK (Япония) класса точности P
- ШВП от PMI/THK (Япония) класса точности C3
- Шпиндель от KASWIN (Южная Корея)
- Маслоотделитель и программируемая задняя бабка в стандартной комплектации
Токарные обрабатывающие центры SPECTR серии TС классическое высокопроизводительное решение для металлообрабатывающего производства. Станки подходят для операций точения, растачивания, сверления, нарезания резьбы.
Токарные обрабатывающие центры SPECTR серии TС применяются во всех отраслях машиностроительной индустрии, в том числе в авиационно-космической, автомобильной и нефтегазовой промышленности для обработки труднообрабатываемых, высоколегированных, жаропрочных сталей и чугуна.
Цельнолитая станина с углом наклона 30 градусов и низким центром тяжести (относительно конкурентов), изготовленная из чугуна марки HT300, который обладает превосходными характеристиками поглощения вибраций, обеспечивает прочную основу для всех узлов станка. После отжига и естественного старения – полностью устраняются внутренние напряжения отливки.
Направляющие отшлифованы с прецизионной точностью за один установ.
Специальная конструкция станины обеспечивает высокую точность и стабильность обработки. Кроме того, угол наклона 30 градусов предоставляет оператору удобный доступ к заготовке и облегчает отвод стружки.
Оси X и Z оснащены высокопроизводительными двигателями подачи Fanuc (Япония).
Направляющие качения класса P (ширина по осям X/Y - 35 / 45 мм) с отличными характеристиками точности и скорости перемещений, позволяют производить скоростную обработку в тяжелых условиях обеспечивая высокую точность в течение всего срока службы.
ШВП от PMI (Япония) с двойным преднатягом исполнены в соответствии с классом точности C3. Диаметр по оси X - 32 мм, по оси Y - 40 мм.
Сверхпрочная конструкция корпуса шпинделя, выполненная из цельного литья Meehanite, сохраняет минимальное тепловое расширение и значительно продлевает срок службы подшипников.
Двухрядные цилиндрические роликовыми подшипниками спереди в сочетании с радиально-упорным двухрядным подшипником сзади, гарантируют высокую жесткость при обработке в тяжелых условиях и как следствие - отличное качество поверхности получаемых деталей.
Станок в стандартной комплектации оснащается ремённым приводом, что оптимально по цене, крутящему моменту и удобству обслуживания.
Система шкивов шпинделя оснащена мощным и надежным электродвигателем переменного тока Fanuc (Япония), обеспечивающим превосходную силу резания в тяжелых условиях.
Ремень шкива типа PK используется для достижения низкого уровня вибрации и шума, а так же отличной шероховатости обрабатываемой поверхности при высоких скоростях вращения.
Сервоприводная револьверная головка (статический инструмент, для моделей TС2000 / TC2500) с гидравлическим тормозом приводится в движение серводвигателем переменного тока с высоким крутящим моментом для быстрого вращения и повторяемости. Конструкция револьверной головки оснащена муфтой большого диаметра, обеспечивающей точное позиционирование и высокую силу зажима.
В базовой комплектации устанавливается обновлённая система ЧПУ FANUC 0i-TF версии Plus расширен функционал:
- Внутренняя память 2 Мб;
- Экран ручной привязки инструмента, для настройки инструмента к детали «вручную», без помощи специальных измерительных щупов;
- Manual Guide (Dynamic Graphic Simulation) - система симуляции обработки (3D).
Панель оператора может поворачиваться на 90 градусов, обеспечивая легкий доступ к управлению во время работы со станком.
Дискового типа предназначен для удаления масляных загрязнений из охлаждающей жидкости.
Диск из нержавеющей стали со специальным покрытием (для удаления масла) вращаясь захватывает масляную пленку с поверхности СОЖ, которая затем удаляется. Очищенная СОЖ попадает обратно в систему циркуляции для дальнейшего использования. Маслоотделитель существенно экономит и продлевает срок службы охлаждающей жидкости в системе.
Для удаления отработанной стружки из зоны резания используется автоматический конвейер (ленточный).
Конвейер включается через M-код или напрямую от пульта управления. С помощью настроек устанавливается интервал и продолжительность работы конвейера для автоматического цикла работы. В комплекте поставляется тележка (корзина) для сбора стружки.
Система измерения инструмента HPMA (Renishaw) позволяет измерить/контролировать размер инструмента перед обработкой, а так же вести мониторинг износа или поломки инструмента в процессе обработки.
Система HPMA полностью исключает из технологического процесса простои станков и брак, связанные с погрешностями при выполнении наладки и контроля инструмента вручную.
Система крепления VDI | Система крепления BMT |
![]() | ![]() |
![]() | ![]() |
Система крепления VDI имеет менее жесткую конструкцию крепления инструментальных блок к револьверной головке, и предназначена для обработки легких сплавов с небольшими припусками. При обработки твердых сплавов срок эксплуатации инструментальных блок значительно уменьшается из-за большой нагрузки на базовые посадочные поверхности.
Система крепления BMT имеет преимущество в жесткости инструментальных блоков к револьверной головке за счет крепления 4-мя болтами к револьверу. Это позволяет производить обработку при тяжелых режимах резания и обеспечивать высокую точность, позволяет достичь высокой производительности и сократить вспомогательное время, т.к. возможно производить обработку с большими припусками.
Преимущества VDI:
- Только один винт для затяжки блока, он прост в установке и быстрее настраивается оператором;
- Меньшие первоначальные инвестиции - стоимость резцедержателя ниже, чем резцедержателя BMT;
- Оператор может регулировать прямолинейность и точность блока.
Преимущества BMT:
- Более жесткий, используется для обработки в тяжелых условиях;
- Точная прямая фиксация, оператору не нужно настраивать прямолинейность блока;
- Больший ресурс блока за счёт равномерного распределения нагрузки при работе (больше упорных подшипников, больше точек крепления к револьверу, короткий вылет хвостовика).
TC2000 (11 / 15 кВт) передаточное отношение 1:1,5 (177 Нм)
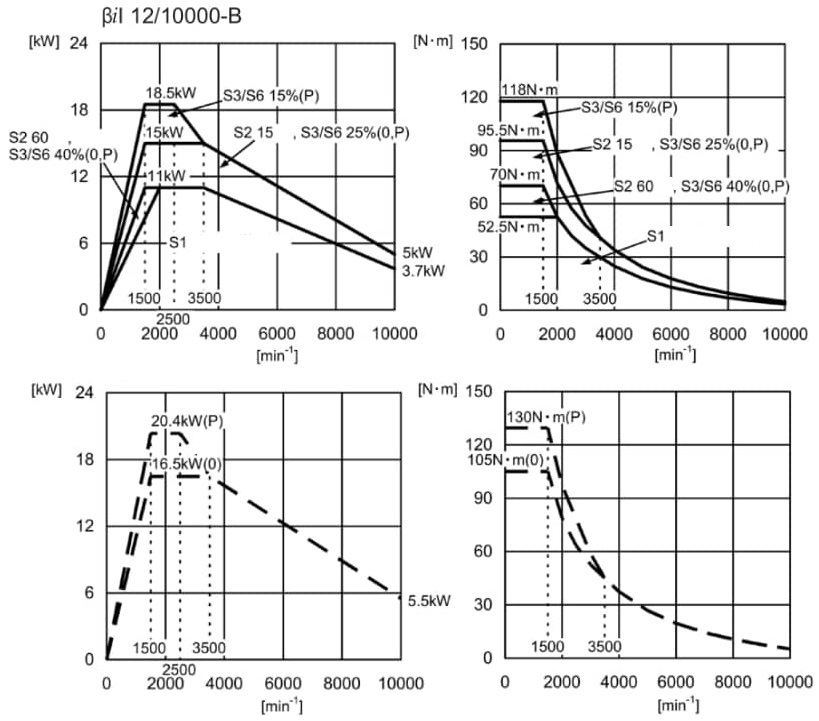
TC2500 (15 / 18,5 кВт) передаточное отношение 1:2 (472 Нм)
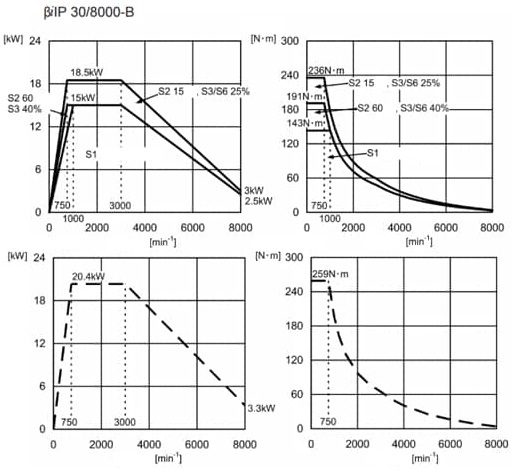
![]() | ![]() |
TC-2000/M
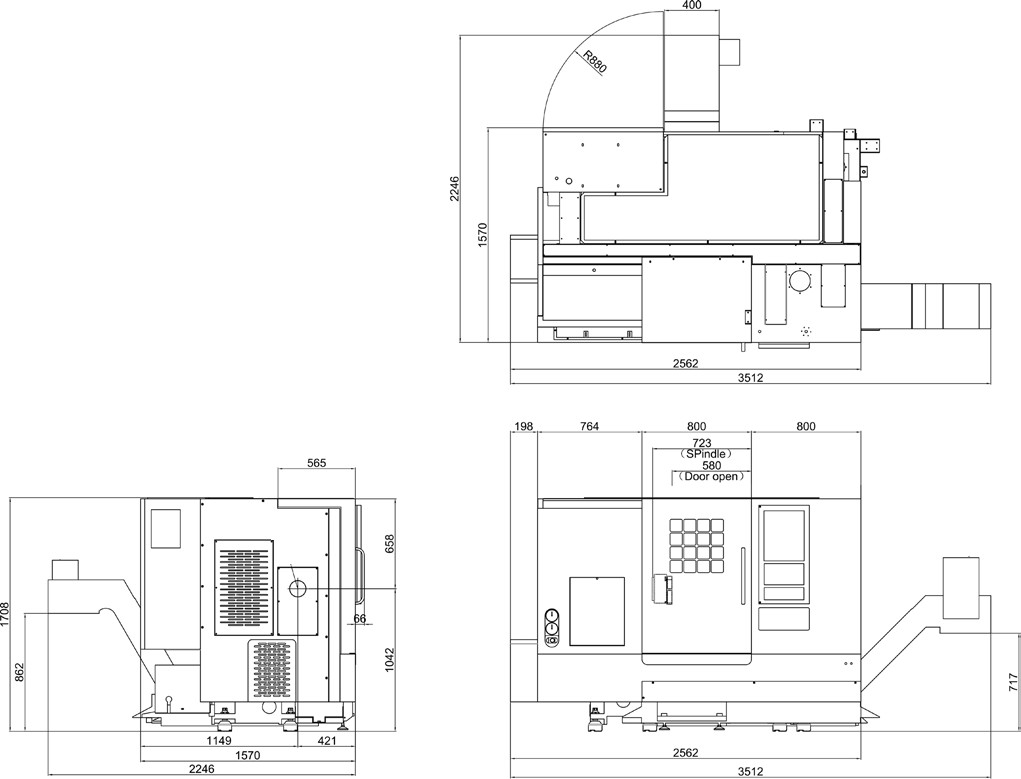
TC-2500/M
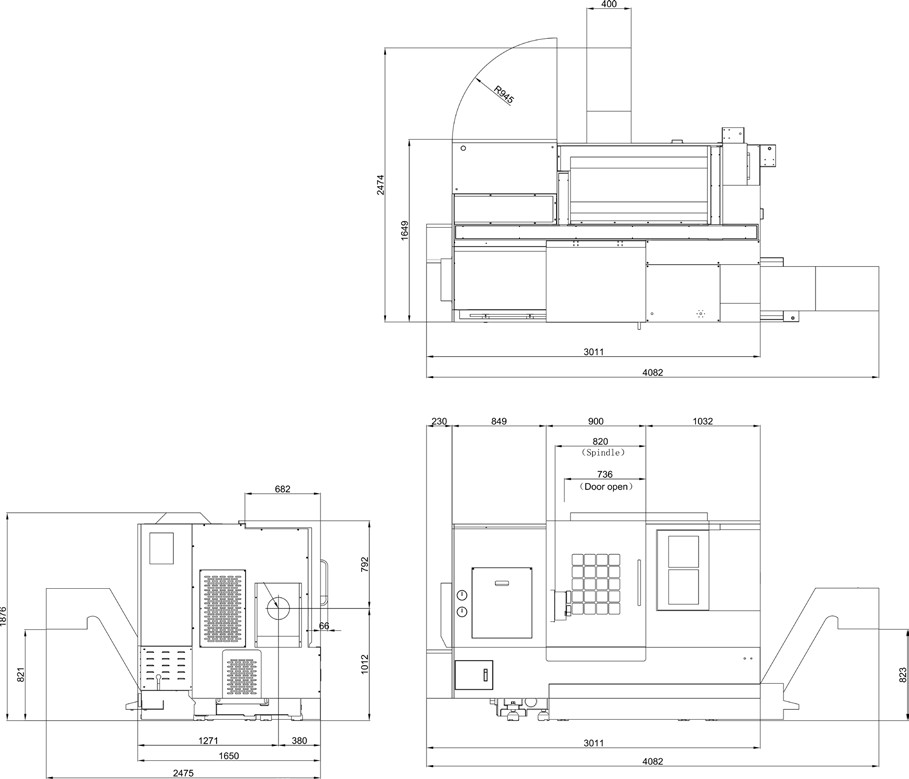